Understanding Porosity in Welding: Discovering Reasons, Effects, and Prevention Techniques
Porosity in welding is a persistent challenge that can significantly influence the top quality and integrity of welds. As experts in the welding industry are well conscious, recognizing the reasons, effects, and avoidance methods connected to porosity is important for attaining robust and reliable welds. By delving into the root creates of porosity, analyzing its damaging effects on weld high quality, and checking out effective avoidance strategies, welders can enhance their knowledge and abilities to create top quality welds constantly. The complex interplay of aspects contributing to porosity calls for a thorough understanding and an aggressive method to make certain successful welding end results.
Common Sources Of Porosity
Porosity in welding is largely created by a mix of variables such as contamination, improper shielding, and inadequate gas coverage during the welding procedure. Contamination, in the form of dirt, oil, or corrosion on the welding surface area, produces gas pockets when heated, resulting in porosity in the weld. Inappropriate shielding occurs when the shielding gas, commonly made use of in processes like MIG and TIG welding, is incapable to completely shield the liquified weld pool from responding with the bordering air, leading to gas entrapment and subsequent porosity. Additionally, poor gas insurance coverage, usually as a result of inaccurate flow prices or nozzle positioning, can leave components of the weld unguarded, enabling porosity to form. These variables jointly contribute to the development of spaces within the weld, compromising its integrity and possibly creating architectural concerns. Understanding and attending to these common reasons are vital steps in avoiding porosity and making certain the high quality and strength of bonded joints.
Impacts on Weld Top Quality
The visibility of porosity in a weld can significantly compromise the total top quality and honesty of the bonded joint. Porosity within a weld produces voids or cavities that weaken the structure, making it more susceptible to fracturing, deterioration, and mechanical failing.
Moreover, porosity can impede the efficiency of non-destructive testing (NDT) strategies, making it testing to identify other problems or gaps within the weld. This can result in significant safety problems, specifically in important applications where the structural integrity of the bonded elements is paramount.
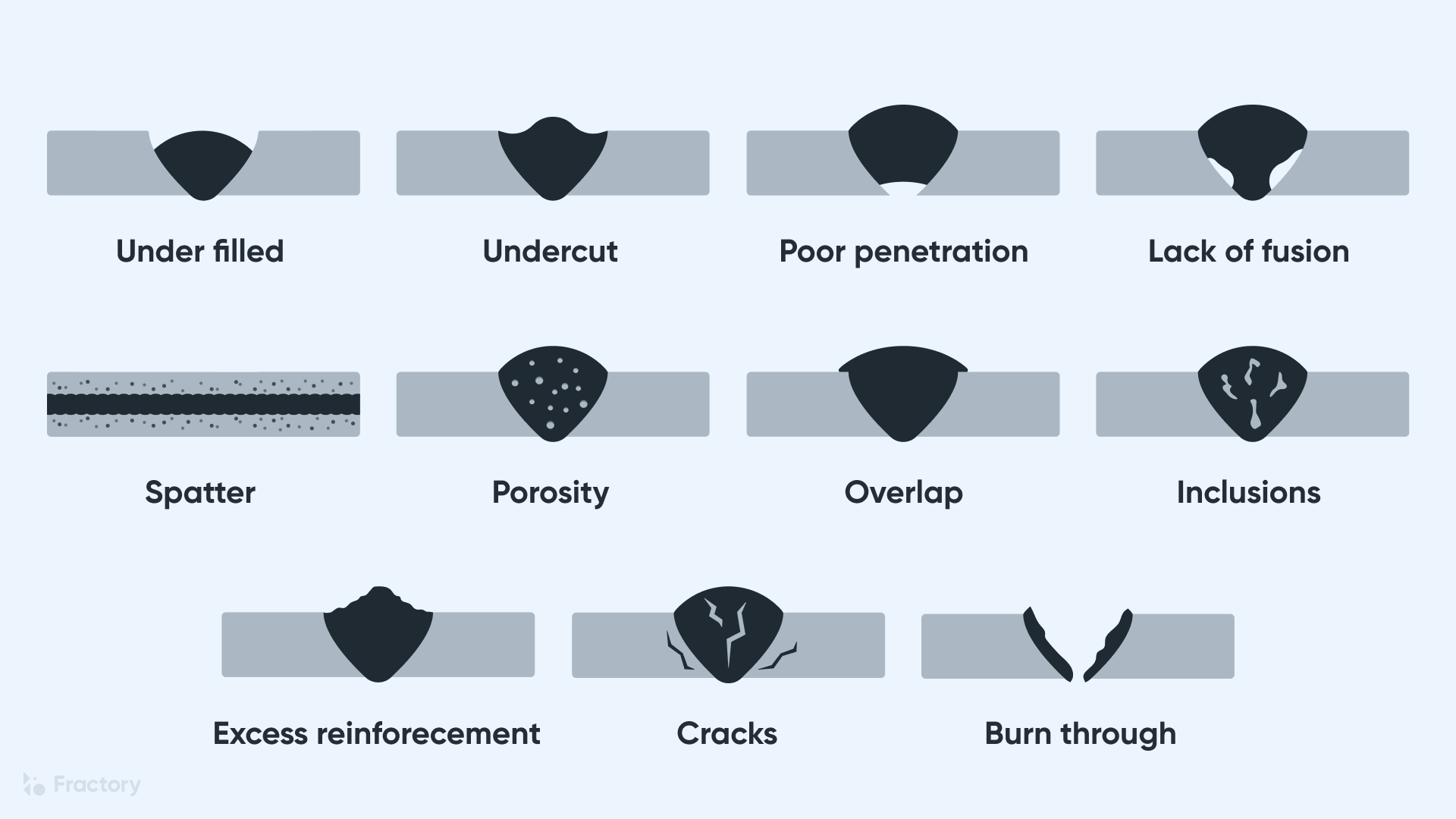
Prevention Techniques Review
Provided the harmful effect of porosity on weld high quality, effective avoidance methods are important to keeping the architectural integrity of learn the facts here now bonded joints. Furthermore, choosing the appropriate welding parameters, such as voltage, existing, and travel speed, can aid reduce the danger of porosity formation. By including these prevention techniques right into welding methods, the occurrence of porosity can be significantly reduced, leading to more powerful and much check here more reputable welded joints.
Relevance of Appropriate Protecting
Proper shielding in welding plays a vital role in stopping atmospheric contamination and making sure the integrity of welded joints. Securing gases, such as argon, helium, or a mix of both, are generally utilized to shield the weld pool from responding with elements in the air like oxygen and nitrogen. When these responsive elements enter call with the hot weld pool, they can trigger porosity, bring about weak welds with minimized mechanical homes.
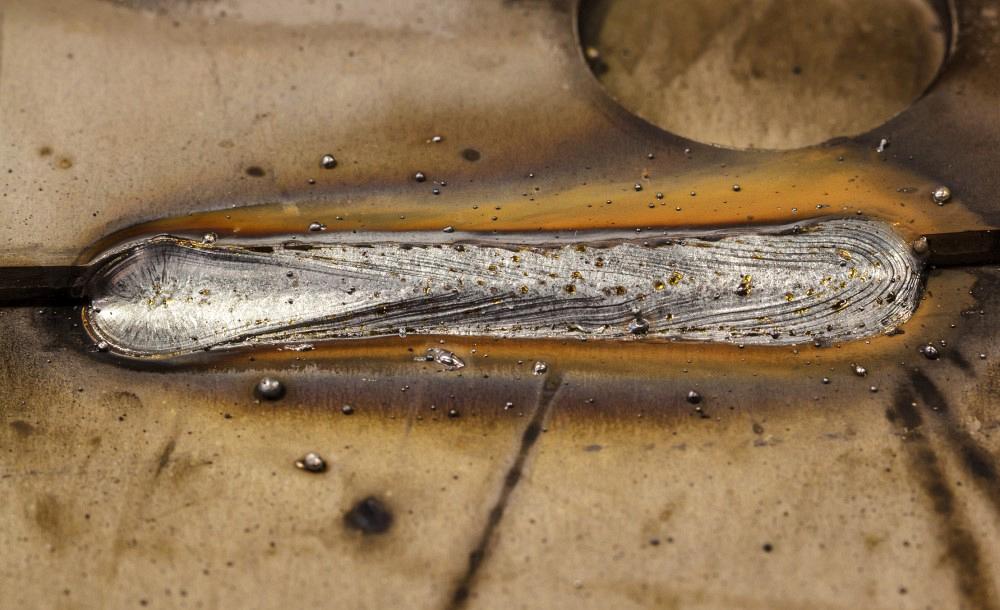
Poor protecting can cause different defects like porosity, spatter, and oxidation, endangering the architectural integrity of the welded joint. As a result, adhering to proper shielding techniques is important to generate top notch welds with very little defects and ensure the long life and integrity of the bonded elements (What is Porosity).
Surveillance and Control Techniques
Just how can welders effectively keep track of and regulate the welding process to make sure optimum results and avoid flaws like porosity? By continuously keeping an eye on these variables, welders can recognize deviations from the optimal problems and make immediate modifications to stop porosity development.

Additionally, implementing proper training programs for welders is necessary for monitoring and controlling the welding process efficiently. What is Porosity. Informing welders on the value of keeping regular criteria, such as correct gas securing and take a trip rate, can aid protect against porosity concerns. Normal analyses and qualifications can additionally ensure that welders excel in tracking and controlling welding processes
Furthermore, making use of automated welding systems can enhance monitoring and control capabilities. These systems can specifically manage welding specifications, reducing the probability of human mistake and making certain constant weld high quality. By incorporating innovative monitoring innovations, training programs, and automated systems, welders can efficiently keep track of and control the welding procedure to decrease porosity flaws and accomplish high-grade welds.
Final Thought
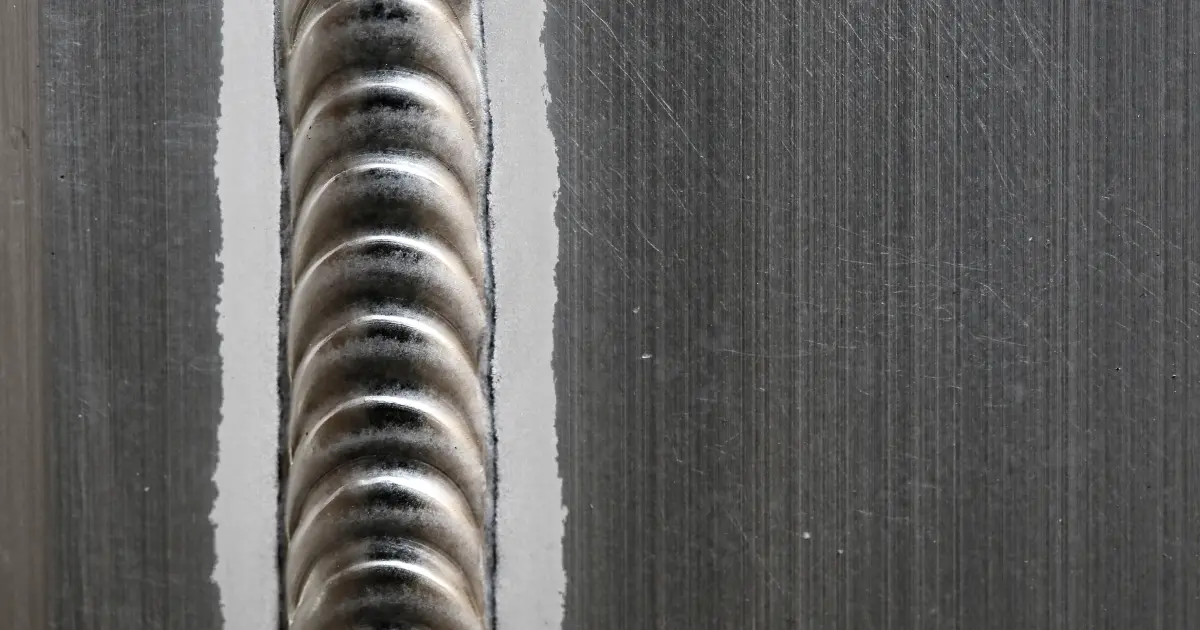